Case Studies: New York
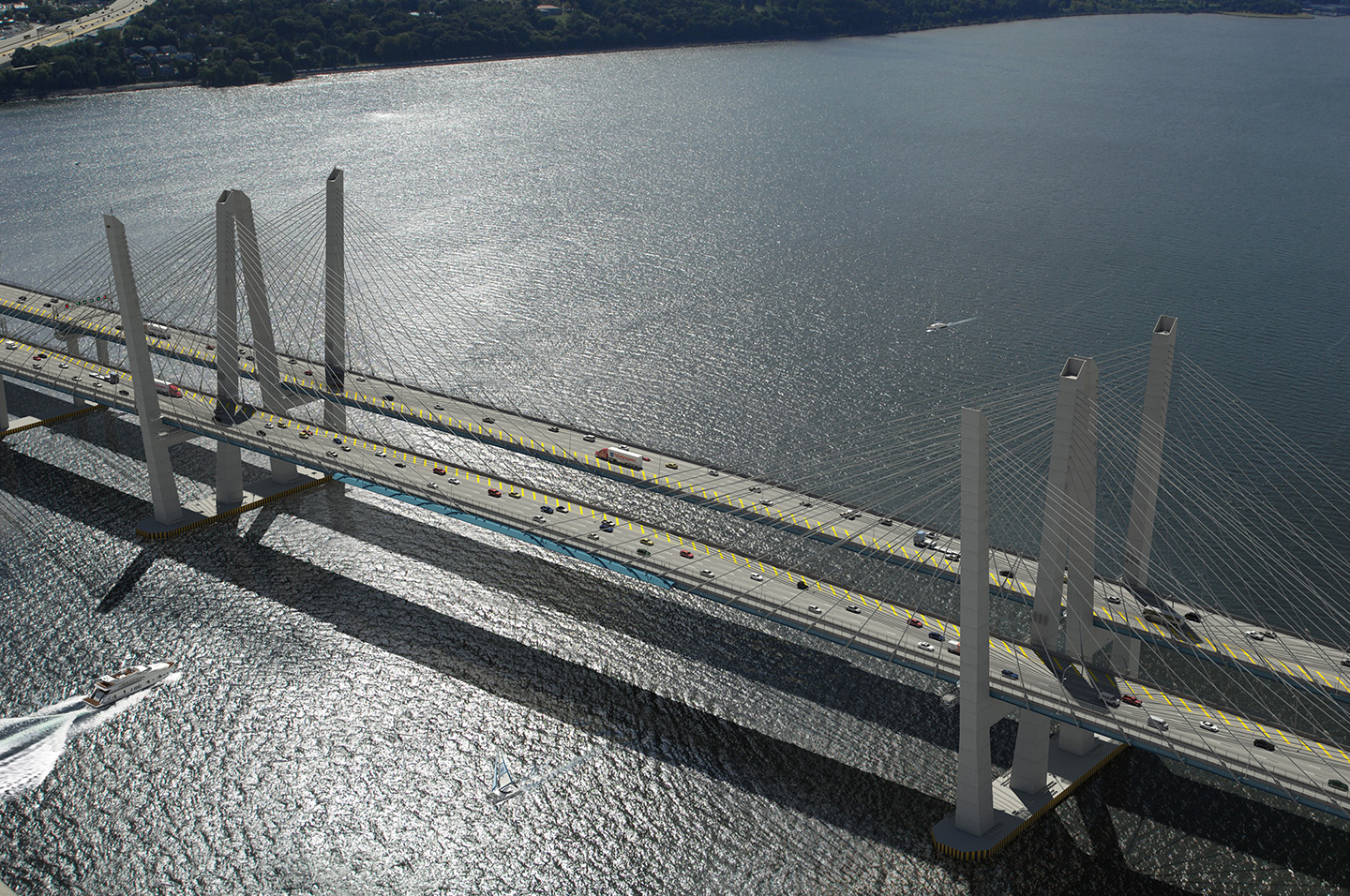
(Photo Credit: New York State Thruway Authority)
New York State Thruway Authority
The New York State Thruway Authority (NYSTA) has specified hot-dip galvanized rebar for all of its bridge decks since 1995. The thruway consists of over 600 miles of toll roads comprising major sections of Interstates 87, 84, and 90, with sections connecting to other interstate highways and toll roads to four neighboring states and Canada. Most of the NYSTA’s 810 bridges are installed in fresh water environments, with the exception of a few that are close to the Atlantic Ocean and qualify as located in a marine environment. In addition to the close proximity to water, the bridges undergo freeze-thaw cycles, and have heavy exposure to deicing salts and industrial pollution, all adding up to a highly-aggressive corrosive environment. The need to protect these bridges from corrosion became a major concern to the thruway authority during the early 1960’s, when maintenance and inspection revealed extensive corrosion to previously installed bridge decks that incorporated bare steel reinforcement in the concrete.
Based on an FWHA endorsement and research conducted by numerous states, the New York Bridge Authority had seemingly solved its corrosion problem by implementing the use of epoxy coated rebar in bridge decks during the early 1980s. In as little as ten years, doubts began to rise regarding the protection provided by these epoxy-coated systems. Within another four years, cracks began to appear in these bridge decks, at which time the thruway authority decided to utilize hot-dip galvanized rebar as its corrosion protection method of choice.
Another concern regarding the performance of epoxy-coated reinforcing steel arose during the NYSTA’s pursuit to find an alternative corrosion protection system. Epoxy coatings were exhibiting inferior bonding to the concrete. When removing sections of concrete from epoxy-coated rebar during a repair of an improperly designed pier, the concrete was easily broken away from the epoxy-coated rebar. By specifying hot-dip galvanized rebar, this problem was eliminated due to the superior bond developed between the galvanized rebar and concrete.
The cathodic and barrier protection provided by hot-dip galvanized rebar has reduced repair costs incurred in handling the rebar in the field. Epoxy-coated rebar was getting damaged in the field due to rough handling at some of the New York bridge installations during the 1980s. Epoxy coatings only supply barrier protection for the underlying steel. If epoxy coatings become damaged during handling or installation, the barrier becomes broken and the corrosion protection for the rebar has been compromised. The superior bond strength and hardness properties of hot-dip galvanized coatings make it tough to damage under any material handling conditions, and if damaged does occur, the exposed bare steel will be protected by the sacrificial cathodic action of the surrounding zinc.
Life cycle cost analysis was performed by the NYSTA to compare the costs of galvanized and other competing coating systems. Initially, the cost of hot-dip galvanized rebar was slightly greater than epoxy coatings and bare steel on a per pound basis. However, the amount of rebar required for an epoxy-coated rebar installation is far greater than for black or galvanized rebar. Lap splices are significantly increased when specifying epoxy coated rebar. This fact alone brings the initial cost of specifying hot-dip galvanized rebar to an extremely competitive position. On a life cycle cost analysis, the maintenance-free hot-dip galvanized rebar is unmatched.
Designing a 100-Year Bridge
The New NY Bridge to replace the Tappan Zee is the largest highway bridge project in North America and continues to make remarkable progress on the Hudson River.
A design lifetime requirement of 100 years led engineers to specify galvanized reinforcing bar throughout the project.
N.Y. State Barge Canal Lock Renovation
Lockport, NY (USA)
The canal filling culverts were lined with galvanized steel plates. The 10 ft. by 7 ft. by 190 ft. culverts were too large to be galvanizing in one piece. Engineers, fabricators and the galvanizer worked as a design team and divided the culvert into quarters and used bracing to keep the plates as true as possible. Plate edges were masked so field welding could be done with minimal fumes in the tunnel. After the first winter’s work and one full season of water and traffic, the culvert looked terrific. New York State Canal Corp. required hot-dip galvanized steel because maintenance would not be necessary for 50 years. A very compressed work schedule with only two winter seasons to work, the canal had to be open spring through fall for traffic and commerce. Original plans were so unreliable that field measurements were required before fabrication could begin, compressing the schedule even further.
Details
Year Galvanized
1999
Sectors
Water & Marine
Environment
Industrial/Urban
Location
Lockport, NY United States
Reasons for Galvanizing
Turnaround Time
Components Galvanized
Handrail, rebar, canal cilling culverts
Team Members
Project Members
Specifier
NYS Canal Corp.
Engineer
NYS Canal Corp.
Fabricator
Technical Erectors
Member Galvanizer(s)
Hubbell Galvanizing