The Galvanizing Process
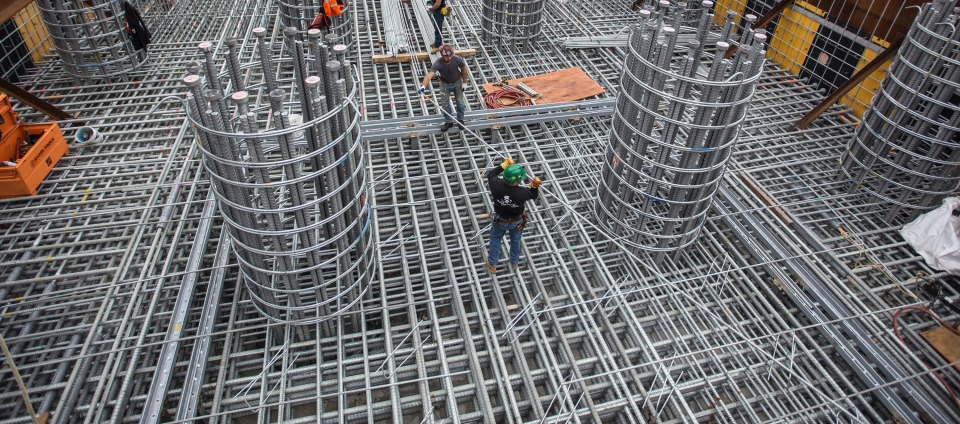
(Photo Credit: New York State Thruway Authority)
Galvanized reinforcing steel is bare reinforcing steel coated with a protective layer of zinc metal. As concrete is porous, the zinc coating serves as a barrier to corrosive elements that migrate to the rebar when embedded in concrete. In addition to the barrier protection that the zinc provides, it also provides cathodic protection where the zinc will preferentially corrode to protect the steel. These two methods of corrosion protection, barrier and cathodic, extend the life of the steel rebar and of the reinforced concrete structure.
Bare reinforcing steel can be zinc coated two ways, either by a continuous galvanizing process (CGR) or by batch hot-dip galvanizing (HDG).
For the continuous CGR process, the bare steel is mechanically cleaned before being rapidly heated in an induction furnace prior to full immersion in molten zinc. Coating thickness is controlled by air wiping. The whole coating process is completed in seconds. For batch HDG rebar, the bare steel is cleaned by dipping in a series of alkali and acid solutions prior to immersion in liquid zinc. Coating thickness is determined by time of immersion. The HDG process takes several minutes.
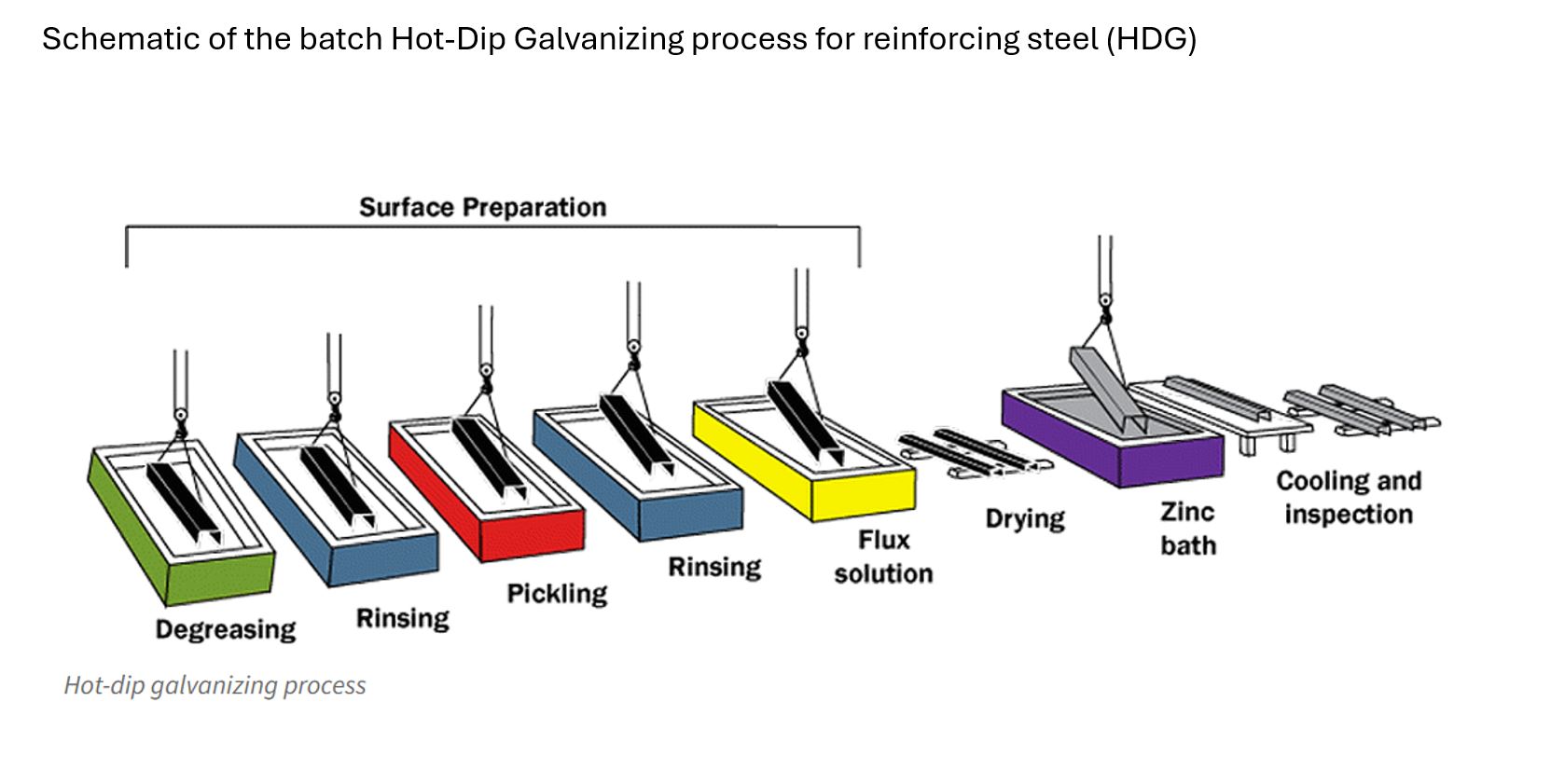
Whether applied continuously or by batch galvanizing, the reaction of the bare steel with liquid zinc produces a metallurgical bond which adheres tightly to the steel. Due to the rapid processing time, the CGR coating consists of a thin intermetallic layer and is mostly pure zinc. HDG rebar is immersed in the molten zinc for several minutes, producing a coating made up of a series of iron-zinc alloy layers with an outer layer of pure zinc.
The figure below is a photo micrograph of a cross-section through the continuous galvanized steel coating and shows a typical coating microstructure. The CGR coating consists of a thin intermetallic alloy layer at the base steel interface covered by a thick layer of pure metallic zinc.
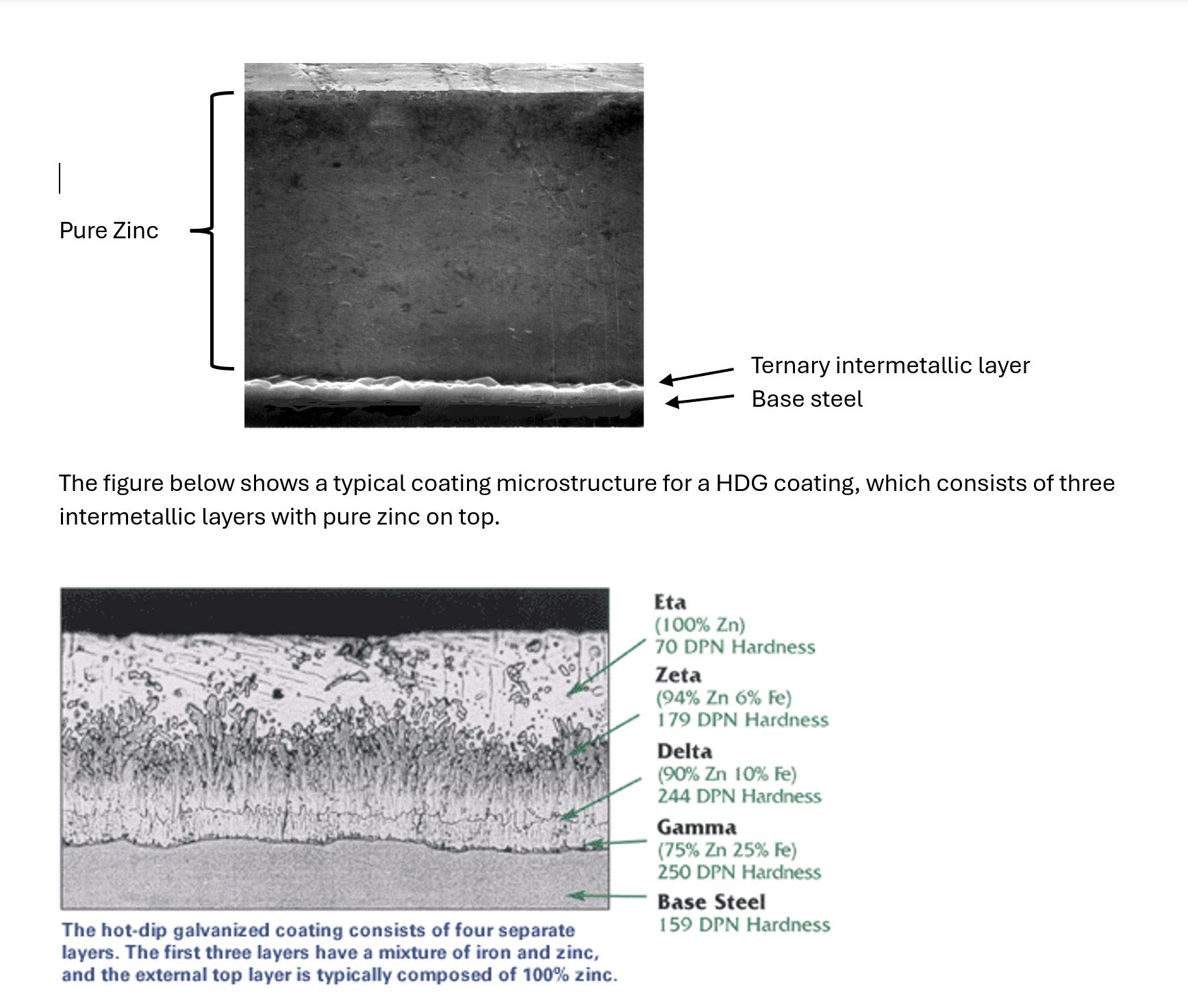
The unique structure of a hot dip galvanized coating offers many important advantages over other coatings. Since galvanized coatings are metallurgically bonded to the underlying steel, the coating has an order of magnitude greater adhesion than, for example, fusion bonded epoxy coatings. In addition, the intermetallic layers of the coating are actually harder than the underlying steel which, combined with a soft outer layer of pure zinc, produces an extremely tough and abrasion resistant coating.
As a result, galvanized rebar can generally be treated in the same manner as uncoated rebar and does not require special handling precautions to protect the coating during handling, transport to, and placement at, the job site. Further, the bond strength of galvanized rebar to concrete is equal to or better than that of uncoated bar. This allows the same reinforced concrete design specifications (bar size, lap lengths, etc.) to be used for galvanized rebar as unprotected bare rebar.
Abrasion Resistance
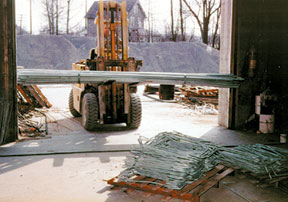
Other coatings damage easily during shipment or through rough handling on the job site. Experts will argue that all organic forms of barrier protection (such as paint) by their nature are permeable to some degree. Galvanized coatings are impermeable. Furthermore, if the galvanized coating is physically damaged, it will continue to provide cathodic protection to the exposed steel. If individual areas of underlying steel or iron become exposed by as much as 1/4″ (6 mm) in diameter, the surrounding zinc will provide these areas with cathodic protection for as long as the coating lasts.
Cathodic Protection

Because zinc is anodic to steel, the galvanized coating provides cathodic protection to exposed steel. When zinc and steel are connected in the presence of an electrolyte, the zinc is slowly consumed while the steel is protected. Zinc’s sacrificial action offers protection where small areas of steel are exposed, such as cut edges, drill-holes, scratches, or as the result of severe surface abrasion. Cathodic protection of the steel from corrosion continues until all the zinc in the immediate area is consumed.
To learn more about cathodic protection view this paper by Gregory Zhang.
Figure 1 below shows how corrosion will begin and immediately progress at a scratch or gap in a paint/epoxy coating. Figure 2 shows how corrosion will be prevented at a scratch or gap in a zinc coating.
Figure 1 | Figure 2 |
![]() |
![]() |