Performance of Galvanized Rebar in Concrete
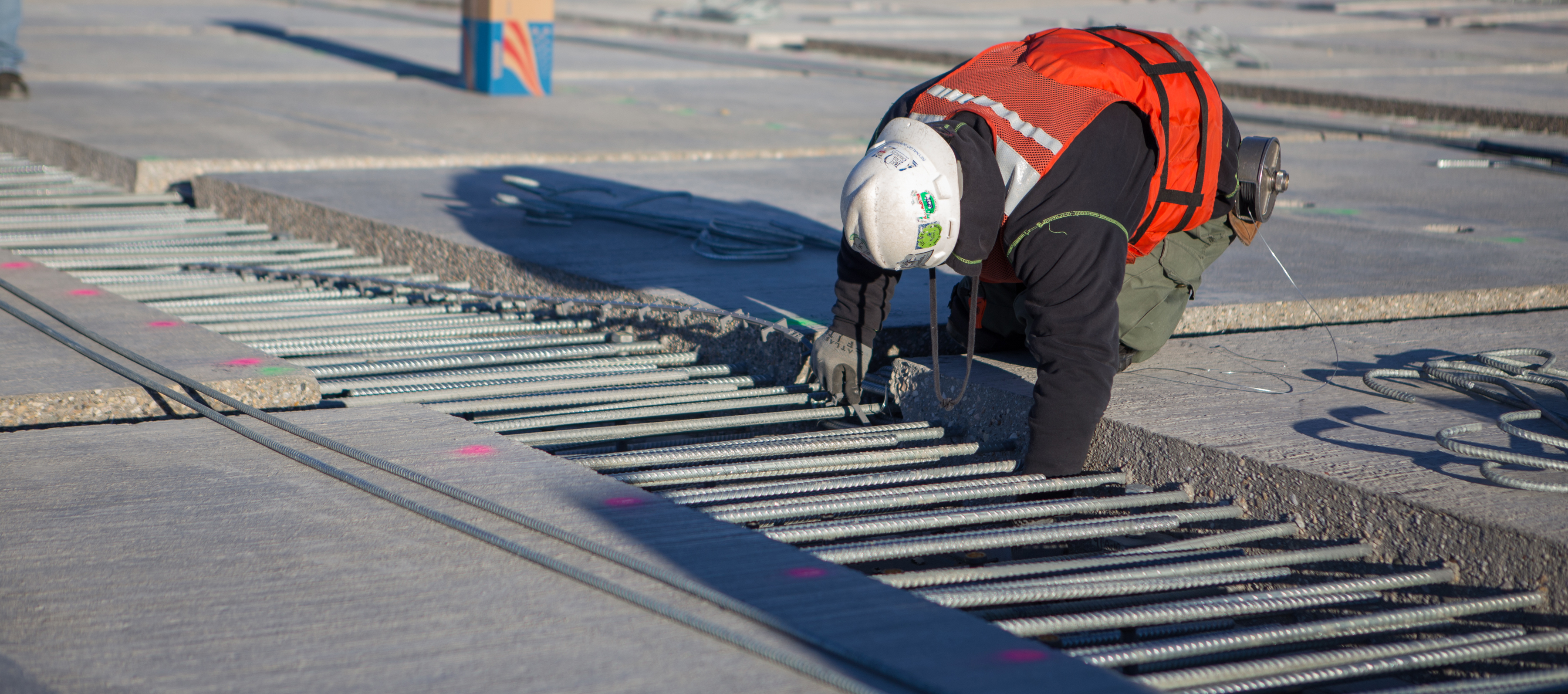
(Photo Credit: New York State Thruway Authority)
Galvanizing provides many levels of protection for concrete reinforcement.
Steel in Concrete
Newly mixed concrete consists primarily of aggregates, cement powder, and water, the latter two components forming cement paste, which soon harden by a process called ‘hydration.’ As the cement paste hardens it binds the aggregate as a solid matrix which gives concrete its load carrying ability and durability. The consumption of the mix water in the hydration-hardening reaction leaves capillary, and ‘gel’ pores in the concrete matrix through which atmospheric gasses, pollutants, and water can penetrate when the concrete is ‘wetted’ by rain, condensation, or spray. The retained water within the pores of the concrete matrix becomes saturated with the chemical components of the cement and forms a highly alkaline solution, with a nominal pH of ~12.5, depending on the specific cement powder used.
Bare reinforcing steel is normally passivated in the initial pH of the contained-water in newly hardened concrete, however, wetting and drying cycles allow for atmospheric gasses including carbon dioxide and sulfur dioxide to dissolve in the pore water, and their acidity in solution begins to lower the pH of the pore water. This process is called carbonation.
Bare reinforcing steel begins to loose its ‘passivation’ or dormancy as the pH surrounding the steel passes below about pH 11.5, and rusting of the steel begins and progresses, the resulting corrosion products take up more space than the steel consumed and this volume expansion within the constraining, rigid concrete matrix, is that substantial stresses are exerted on the surrounding concrete.
In addition to the lowering of the pH of pore space water below the threshold of passivation of imbedded bare steel, chloride ions from the structure surroundings, also are dissolved in the pore water, and once permeation down to the steel surface, further act to destroy the passivation of the embedded bare steel. The time elapsed before the combination of acidic atmospheric components and chlorides permeate to the embedded steel surface is a function of the environment, wetting cycles, porosity and composition of the concrete, and the length and difficulty of traversing the labyrinthine path to the bar surface. This latter factor is partly related to the ‘depth of cover’ of the embedded bar.
How Zinc Protects Rebar in Concrete: Higher Chloride Corrosion Initiation Threshold
The corrosion protection afforded by galvanized rebar in concrete is due to a combination of beneficial effects. Of primary importance is the substantially higher chloride threshold (2-4 times) for zinc coatings to start corroding compared to uncoated steel. In addition, zinc has a much greater pH passivation range than steel, making galvanized rebar resistant to the pH lowering effects of carbonation as the concrete ages. Even when the zinc coating does start to corrode, its corrosion rate is considerably less than that of uncoated steel.
Why Galvanized Rebar Maintains Concrete’s Integrity: Corrosion Product Migration and Concrete Matrix Densification
Zinc’s corrosion products are loose, powdery minerals that are less voluminous than iron corrosion products and are able to migrate away from the galvanized rebar surface into the adjacent concrete matrix. As a result, corrosion of the zinc coating causes very little physical disruption to the surrounding concrete. The elemental map (left) is evidence of this migration. The white spots in the concrete indicate zinc oxide which has migrated away from the galvanized rebar/concrete interface.
There is also evidence to suggest that the diffusion of zinc’s corrosion products helps fill pore spaces at the concrete/rebar interface, making this area less permeable and helps to reduce the transport of aggressive species such as chlorides through this interface zone to the zinc coating. The reactions between zinc and concrete, and the resulting corrosion product diffusion, also explains why galvanized rebar has such good bond strength with concrete.
Tolerance of Lower pH due to Carbonation
Zinc remains passive at significantly lower pH levels than for black steel (9.5 versus 11.5) making galvanized rebar far less susceptible to corrosion due to carbonation of the concrete.
Zinc’s Initial Reaction in Fresh Concrete
Zinc reacts with wet concrete to form calcium hydroxyzincate accompanied by the evolution of hydrogen. This corrosion product is insoluble and protective of the underlying zinc (provided that the surrounding concrete mixture is below a pH of about 13.3). Research has shown that during this initial reaction period until coating passivation and concrete hardening occurs, some of the pure zinc layer of the coating is dissolved. However, this initial reaction ceases once the concrete hardens and the hydroxyzincate coating has formed. Studies of galvanized rebar recovered from field structures indicate
that the coating remains in this passive state for extended periods of time, even when exposed to high chloride levels in the surrounding concrete.
For concretes of high pH, or where some background chlorides are expected, the zinc surface can be passivated, using a range of proprietary post treatments, as a safeguard against excessive hydrogen evolution that may, in serious cases, reduce the pullout strength of the bar. For normal concrete conditions, research has shown no statistical difference in bond strength between galvanized rebar that was passivated and not passivated.
Corrosion Model
Zinc coatings have a higher chloride (Cl -) corrosion threshold (2-4 times) than that of uncoated steel, significantly extending the time until corrosion initiation. Once corrosion of the zinc coating does occur, the properties of the corrosion products and their ability to migrate into the concrete matrix reduces stress generation in the surrounding concrete, further extending the life of the reinforced concrete structure. Black and galvanized rebar corrosion performance in concrete can be shown graphically at right.
Accelerated Testing/Salt-Spray
Efforts have been made in many zinc-coated steel applications to develop the correct test method to determine a proper “accelerated” lifetime. One test for corrosion prevention systems in the United States is ASTM B117. ASTM Committee G-1 on Corrosion of Metals has jurisdiction over the salt spray standards B117 and G85. The Committee passed the following resolution regarding the use of B117: “ASTM Committee G-1 on the Corrosion of Metals confirms that results of salt spray (fog) tests, run according to ASTM standard designation B117, seldom correlate with performance in natural environments. Therefore, the Committee recommends that the test not be used or referenced in other standards for that purpose, unless appropriate corroborating long-term atmospheric exposures have been conducted.”
“ASTM B117 and B368 are best used as quality control tests assuring that the day-to-day quality of products and manufacturing processes are optimized. There are a number of other corrosion tests which can be used for predicting performance in service.”
Salt spray tests cannot be used to accurately test zinc-coated steel because they accelerate the wrong failure mechanism. Without a proper wet/dry cycle, the zinc coating cannot form patina layers. The absence of a patina layer allows constant attack of the zinc metal and gives a very low prediction of the zinc coating lifetime.