The existing Governor Malcolm Wilson Tappan Zee Bridge bridge opened to traffic in 1955 and is a vital artery for residents, commuters, travelers and commercial traffic. Bridge traffic has grown to about 138,000 vehicles per day, far more than the Tappan Zee was designed to support. Heavy traffic, narrow lanes and the lack of emergency shoulders can create unsafe driving conditions. As a result, the bridge has twice the average accident rate per mile as the rest of the 574-mile Thruway system. Hundreds of millions of dollars have been spent to maintain the structure in recent years. The cost of maintaining the current bridge for the foreseeable future rivals the cost of a new bridge, with no improvements to current traffic conditions.
The New NY Bridge will mean less congestion and frustration for motorists, with eight general traffic lanes, breakdown/emergency lanes, and a state-of-the-art traffic monitoring systems. The new crossing will also be mass-transit ready, with space for Bus Rapid Transit as well as a design that can accommodate future light rail or commuter rail. The bridge will also feature a shared use path for pedestrians and cyclists.
Steel bars that reinforce the new bridge’s concrete structures are coated with a protective zinc coating.
Over 60 million pounds of steel bars will fortify the new bridge, more than three times as much steel as is in the iconic Eiffel Tower in Paris. Each of the reinforcing steel bars, called rebar, is treated through a process called “hot-dip galvanization” that provides additional protection against rusting.
Rebar, formed into interwoven support networks deep inside the bridge’s concrete structures, plays a crucial role in the strength of the new crossing – from its deep foundations to the top of its 419-foot towers. Protecting the steel is especially important given the bridge’s location in the brackish waters of the Hudson River. The semi-salty water can penetrate concrete, causing the rebar to rust or otherwise degrade. Galvanizing the rebar provides a barrier and sacrificial protection to delay potential corrosion, thereby extending the life of the structure.
The galvanization process begins with carefully cleaning each steel bar with an acidic solution, removing all traces of grease and dirt from the metal. The steel is then thoroughly rinsed before it is dipped in a hot bath of molten zinc. The two metals, steel and zinc, are chemically bonded, sometimes through an electric current that is run through the bath. This creates a crystalline skin over the rebar that acts as a barrier between the steel and the elements.
Once fabricated, galvanized rebar is brought to either the project site or a precast concrete facility by truck or barge, where the bars are tied together to form the skeletal support of the new bridge’s decks, piles, pile caps and footings, columns and pier caps. The networks of rebar are assembled according to detailed specifications and are carefully inspected in the field to ensure proper placement.
The cages of rebar are then encased in concrete, forming the bridge’s critical structures, including the main span towers, approach span piers, concrete roadway deck and bridge abutments.
Rebar galvanization is another of the many factors that will ensure the bridge serves generations of travelers over the next 100 years and beyond.
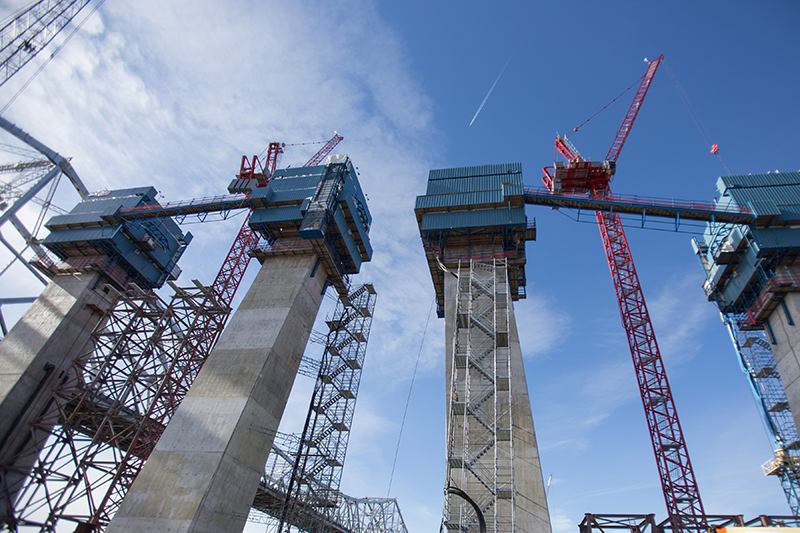
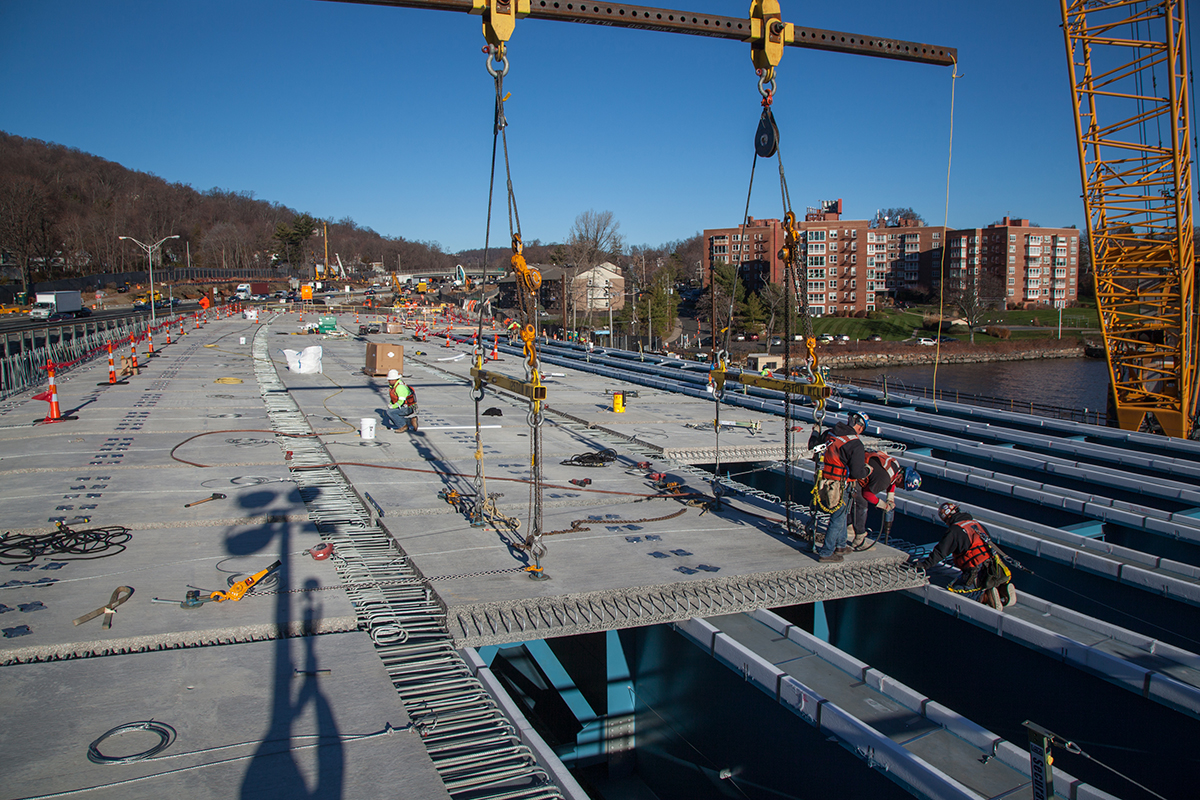
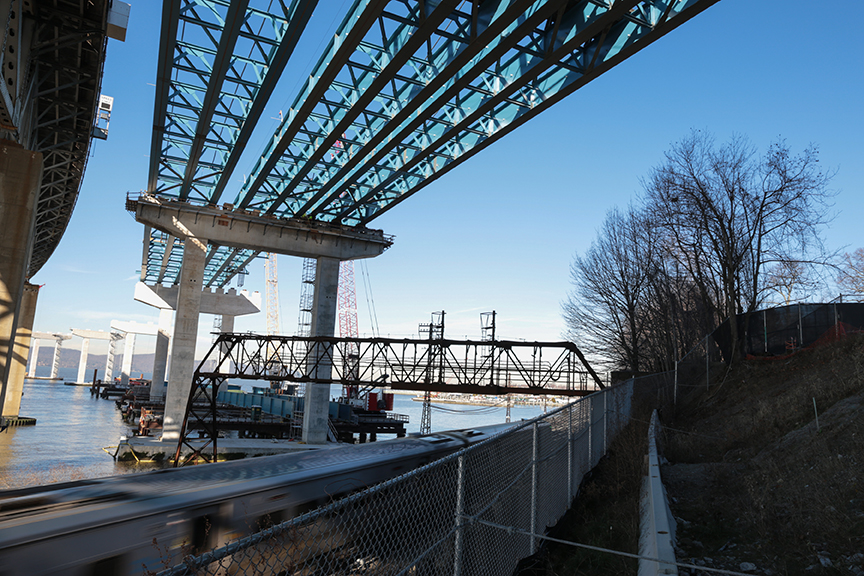
(All images courtesy of New York State Thruway Authority)