Galvanized Rebar: It Works
Corrosion damage to reinforced concrete structures in the United States costs an estimated $20 billion annually. This figure is expected to grow by $500 million each year as existing infrastructure continues to age. Addressing corrosion after construction is expensive and disruptive as all or part of the structure needs to be closed periodically for maintenance and repair. Failure to properly address corrosion can also lead to catastrophic structural failures with potentially deadly consequences.
Galvanizing, the process where steel parts are immersed in a bath of molten zinc, has a proven track record and should be your first choice in corrosion protection – because it works.
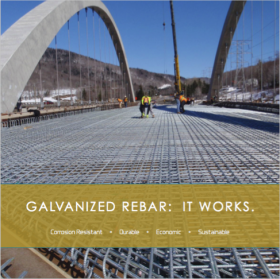
Galvanized Steel Reinforcement in Concrete
This reference provides a detailed resource covering all aspects of galvanized reinforcing bar. Both serviceability and durability aspects are well covered, with all the information needed maximize the life of structures constructed from it. Containing an up-to-date and comprehensive collection of technical information and data from world renowned authors, it is a valuable source of reference for academics, researchers, students and professionals. Read the summary.
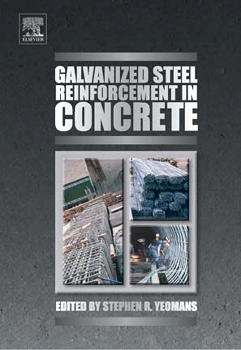
Hot Dip Galvanized Reinforcing Steel: A Concrete Investment
Reinforced concrete is one of the most widely used modern construction materials. It is inexpensive, readily available, has a range of attractive properties and characteristics and is suitable for a variety of building and construction applications. It is also used in a number of exposure conditions, which in some cases highlights one of the main weaknesses of reinforced concrete: the potential for the steel reinforcement (rebar) to corrode, resulting in staining, cracking and failure of the surrounding concrete. This brochure highlights the performance of galvanized rebar in concrete along with projects that have benefited from its use.
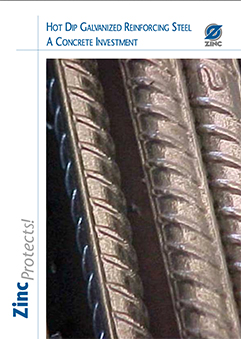
Bond and Slip of Coated Reinforcement in Concrete
Authors: O. A. Kayyali and S. R. Yeomans
Concrete beams reinforced with black, epoxy-coated, or galvanized steel were tested to failure in flexure and the slip of the reinforcement was monitored. While there was clear evidence of the influence of bar deformations on the bond capacity of beams reinforced with smooth compared to ribbed black steel bars, the majority of the work concentrated on comparing the load-slip behavior of ribbed bars as affected by the presence of surface coatings. Overall, the results of this work indicated that there was no significant loss in bond with the use of galvanized bars, though a significant reduction was observed with epoxy-coated bars.
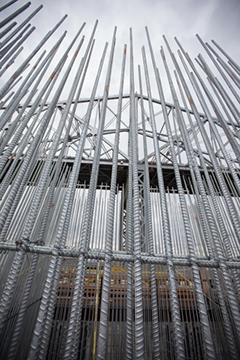
Comparative Studies of Galvanized and Epoxy-Coated Steel Reinforcement in Concrete
Author: S. R. Yeomans
Comparison of the corrosion performance and pullout strength of black, hot-dip galvanized, and fusion-bonded epoxy-coated steel reinforcement in concrete have been undertaken. Accelerated exposure testing confirmed that zinc coating was able to considerably delay the onset of corrosion and epoxy coating effectively eliminated corrosion provided the coating was not damaged. Pullout testing revealed that there is no significant difference in the ultimate bond strength of black, epoxy-coated, or galvanized deformed bars. The passivation of the galvanized reinforcment with concrete did not conclusively improve the bond strength.
Further Studies of the Comparitive Properties and Behavior of Galvanized and Epoxy Coated Steel Reinforcement
Author: S. R. Yeomans
Further studies of the characteristics and properties of fusion-bonded epoxy-coated steel reinforcement and hot-dip galvanized reinforcement have been undertaken. The comparative corrosion performance of black, galvanzed, and epoxy-coated reinforcement was investigated in which the influence of exposed cut ends of coated reinforcement and the repair of cut ends was examined. Pullout testing of black, galvanized, and epoxy coated plain rebar was also done, as well as pullout tests using galvanized plain reinforcement in which varying amounts of chromate ions were added to the concrete via mix water additions. Where the cut ends of coated reinforcement were repaired, the epoxy-coated bars showed many sites of local breakdown of the repair and corrosion of the underlying steel. In contrast, the repairs to the galvanized bars performed very satisfactorily with little or no evidence of breakdown of the repair even in the wet and dry salt water environment.
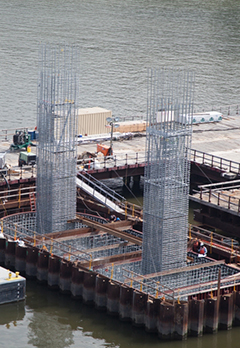
Considerations of Characteristics and Use of Coated Steel Reinforcement in Concrete
Author: S. R. Yeomans
A review is presented of important considerations in the manufacture, specification and performance of two types of coated steel reinforcement: galvanized and epoxy-coated. Epoxy-coated reinforcment solely lies on its ability to provide a barrier between the base steel and corrosive elements. If the coating becomes damaged, the barrier is broken and corrosion will soon commence and spread across the bar. Galvanized reinforcement provides both barrier and cathodic protection, which allows the coating to protect small areas where the coating has become damaged. The results of a program of acclerated corrosin testing of black steel, galvanized steel, and epoxy-coated steel are presented in this paper. Under teh same conditions in equivalent concrete, galvanized reinforcment tolerated chloride levels 2.5 times higher than epoxy, while delaying the onset of corrosion by a factor of 4-5 times that of the epoxy coating.
Corrosion of the Zinc Alloy Coating in Galvanized Reinforced Concrete
Author: S. R. Yeomans
The corrosion of galvanized reinforcement in concrete is a multi-stage process. After a generally long period to the initiation of corrosion, dissolution of the galvanized coating commences with the loss of the outer pure layer of zinc, followed by slow dissolution of the underlying zinc-iron intermetallic layers. Corrosion of the parent steel does not commence until the zinc alloy layers are completly lost from extensive areas of the bar surface. This process results in the well documented delay int he appearance of corrosion of zinc coated steel reinforcement in concrete. The zinc corrosion products appear to cause little or no disruption to the cover concrete and have been observed to fill microcracks and small voids in the matrix, resulting in a an apparent densification of the cement matrix, at distances up to 0.5 mm from the bar interface.
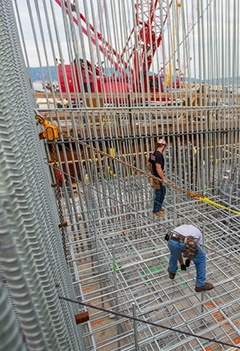
Field Performance of Epoxy-Coated Reinforcing Steel in Virginia Bridge Decks
Author: W.A. Pye
The corrosion protection performance of epoxy-coated reinforcing steel (ECR) was evaluated in 18 concrete bridge decks in Virgina in 1997. The decks were 2 to 20 years old at the time of investigation. The concrete bridge deck inspections included crack survey and cover depth determination in the right traffic lane. The ECR inspection consisted of visual examination and damage evaluation, coating thickness and adhesion determination. The condition of the steel underneath the epoxy coating was also evaluated. Adhesion loss of the epoxy coating to the steel surface was detected for 4 years old bridge decks. The epoxy coating had debonded from the reinforcing bar before chloride arrival. Visible signs of a possibility of a corrosion process underneath the coating suggest that ECR will not provide any or little additional service life for concrete bridge decks in comparison to black steel. Other systems, which will provide longer protection with a higher degree of reliability against chloride induced corrosion of steel in concrete, should be considered.
Corrosion Protection Service Life of Epoxy-Coated Reinforcing Steel in Virginia Bridge Decks
Authors: M. C. Brown and R. E. Weyers
The corrosion protection service life extension provided by epoxy-coated reinforcement (ECR) was determined by comparing ECR and bare steel bars from 10 Virginia bridge decks buildt between 1981 and 1995. Altogether, 141 drilled cores, 4 inches in diameter, were employed in this study. The corrosion service life extension attributable to ECR in bridge decks was found to be approximately 5 years beyond that of bare steel and, therefore, ECR is not a cost-effective method of corrosion prevention for bridge decks.
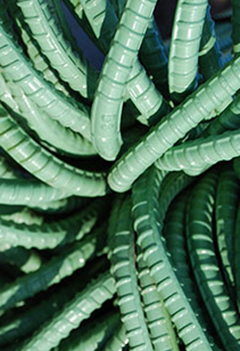
Research and Update on Galvanized Reinforcing Steel
Author: T.J. Kinstler
Experimental and anecdotal evidence have shown the efficacy of galvanized reinforcing steel in concrete applications. However, the mechanism for this performance has not been collectively explored. This paper reviews significant experiences with galvanized rebars, and synthesizes these experiences with a newly reported investigation into a paradigm which is consistent with demonstrated field and laboratory behavior. The superior performance of galvanized bars versus balck bars results from a higher threshold for corrosion initiation, reduced corrosion kinetics, and a lowering of stresses induced in the concrete as a result of the mobility of zinc corrosion products.
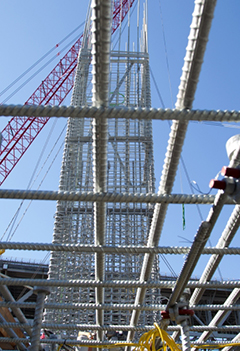
Hot-Dip Galvanized Reinforcing Steel: A Specifiers Guide
This 16-page publication from the American Galvanizer’s Association discusses rebar corrosion, hot-dip galvanizing, and how galvanized rebar performs in concrete including design, specification, fabrication, and installation concerns.
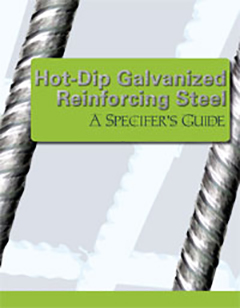
Galvanized Rebar: Lowest Cost of Ownership in Reinforced Concrete Bridges
This technical brochure details a study conducted by Virginia Tech University professor Richard Weyers, sponsored by IZA. Weyers examined the diffusion of chloride into concrete decks and its effects on service life for epoxy-coated rebar, batch galvanized steel rebar, and 316LN stainless steel rebar in each of Virginia’s six different climactic zones. Findings clearly demonstrated that galvanized steel rebar provides the most cost-effective protection for reinforced bridge decks with a 100-year life.
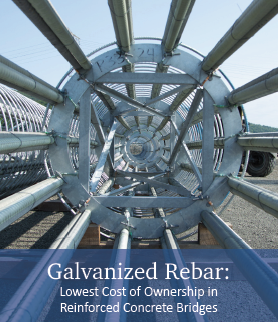